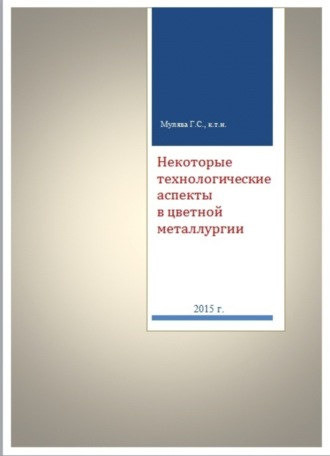
Некоторые технологические аспекты в цветной металлургии
1.6.1. Технологическая схема производства меди
Схема производства меди пирометаллургическим способом – окислительной плавкой в отражательной печи и (или) обжигом в печах КФП медных сульфидных концентратов с вовлечением в переработку лежалых (отвальных, конвертерных) шлаков, приведена на рисунке 1.33.
Рис. 1.33 Технологическая схема получения меди из концентратов
с вовлечением в переработку шлаков, содержащих
Cu 0,8-1,2 %; с учётом представлений о процессе в [ 1 ]
1.6.2 Известные способы переработки медных сульфидных концентратов и потери меди и драгоценных металлов со шлаками.
Рассмотрим ряд способов переработки медных сульфидных концентратов, близких к практическому применению, или – уже реализованных на практике.
В [2] предложено проводить сульфатизирующий обжиг медных концентратов при (500 – 600) 0С в течение (90 – 180) мин и затем выщелачивать огарок раствором серной кислоты или водой с отделением кека и фильтрата. Из последнего электролизом выделяют медь, а кек шихтуют с окислителем и хлоридами щелочных и щёлочноземельных металлов, проводят термообработку при (450 – 550) 0С, полученный спёк выщелачивают раствором соляной кислоты и из полученного фильтрата выделяют сорбцией благородные металлы.
Недостатком этого способа является предложение использовать для выщелачивания меди серную кислоту, что переведёт в раствор значительные (до 15 г/л) массовые доли железа (III), а это усложнит процесс электролиза. Не указаны режимы выщелачивания. Спекание кека с хлоридами металлов приведёт к одновременной хлорид возгонке токсичных элементов из концентрата (например, мышьяка).
Известен и нашёл практическое применение процесс переработки медных концентратов смешиванием их с кварцевым флюсом и плавкой шихты с получением штейна и шлака, которые разделяют, штейн конвертируют, а шлак направляют в отвал, см. например [ 3 ].
В настоящее время также реализован способ переработки концентратов медных сульфидных руд с добавлением шлаковых медьсодержащих концентратов и плавлением их с флюсом. Способ включает добавление в шихту шлаковых сульфидных медь-содержащих концентратов, полученных флотационным обогащением техногенных промпродуктов – медьсодержащих шлаков с исходным содержанием меди (0,8 – 1,2) %, [4], см выше, п.1.6.1.
Однако, как удалось установить, минералогический анализ шлаковых концентратов показывает на наличие в них преимущественно следующих форм меди: низшего сульфида – халькозина (Cu2S) и высших: ковеллина (CuS), халькопирита (CuFeS2) и борнита (Cu5FeS4) с примерным соотношением по меди 1 : 1 : 2.
При окислительной плавке шихты по [ 3 ], например в условиях малоподвижного слоя в отражательной печи, первичные сульфиды меди и железа, как и халькопирит, при дальнейшем нагревании становятся основой штейна. Из данных термодинамических расчётов следует, что с наибольшей вероятностью будет подвержен сульфатизирующему обжигу в этих условиях лишь борнит, например:
Cu5FeS4 + 4,25 О2 = 2 CuO + 3CuSO4 + 0,5 Fe2 (S O4)3 + SO2. ( 1 )
При (400– 600) 0С оксид меди CuO, продукт реакции ( 1 ), сульфидизируется пиритом, содержащемся в концентрате сульфидных руд:
2 CuO + 2 Fe S2 = Cu2 S + 2 Fe S + SO2. ( 2 )
При температурах (640-770) 0C, когда уже значительно израсходуется пирит, разлагается сульфат меди окислившегося борнита с образованием «вторичного» оксида меди:
CuSO4 = CuO + SO3 . ( 3 )
Часть этого оксида меди при температурах 700 0C и более легко формирует растворимые в шлаке ферриты меди, например CuO*Fe2O3, что является причиной повышенных потерь меди с железистыми шлаками медного производства, когда совместно с рудным, перерабатывается и шлаковый концентрат.
Второй причиной потерь меди (и. соответственно, золота и серебра) со шлаками по этому способу, по нашему мнению, является их повышенная вязкость, причиной чего служит добавление в них тугоплавкого магнетита
(tпл = 1520 0C), присутствующего в шлаковых концентратах в количестве (12 -15)%. Стремление снизить вязкость шлаков потребует увеличения температуры в печи и, следовательно, приведёт к повышенному расходу природного газа. Косвенно это также может привести к уменьшению межремонтного срока эксплуатации печи.
1.6.3 Минералогический анализ сульфидных медных концентратов и
металлургических шлаков. Рациональный состав концентратов
В процессе металлургического передела медных руд в шлаках остается некоторое количество меди. В настоящее время часть этой меди с извлечением до (65 – 70) % переводят флотационным обогащением в шлаковый концентрат с содержанием металла 14-18 %, [ 5, 6 ]. При содержании меди в отвальных шлаках (0,8 – 1,2) %, что характерно при разработке "старых" отвалов, получают относительно высокие показатели флотационного процесса.
В работе [7] приводятся результаты минералого-геохимических исследований шлаков и их концентратов, полученных при производстве меди из полиметаллической руды одного из месторождений Средней Азии, выявлены минеральные формы нахождения медьсодержащих соединений в них и установлены количественные соотношения. В настоящей главе, основываясь на материалах [7] и с привлечением других данных, исследован переход сульфидов меди из рудных форм в шлаковые и предложен возможный механизм такого перехода.
Рациональные составы рудного и шлакового концентратов показывают (см. таблицу 1.7), что при примерно одинаковых массовых долях меди в концентратах, минеральные формы нахождения их различны по количественному составу. В первую очередь обращает на себя внимание то, что в рудном концентрате относительно высокое содержание халькопирита (28,1%) в то время как для шлакового концентрате характерен борнит (почти 15 % при содержании борнита в рудном концентрате всего 1,26%). В аншлифах проб шлакового концентрата хорошо видно (см. рисунок 1.34), что в сформированных медно-шлаковых включениях тесно соседствуют халькопирит и борнит. Это, как и уменьшение халькопирита в шлаковом концентрате (табл. 1.7), говорит о том, что возможным продуцентом борнита в шлаке является металлургическая реакция с участием халькопирита и сульфидной формы меди в штейне. Например:
CuFeS2 + 2Cu2S = Cu5FeS4. ( 4 )
Подробный минералогический анализ проб рудного и шлакового концентратов, а также шлака, позволил составить таблицу минеральных составов этих продуктов (таблица 8). Отметим близкое совпадение данных этой таблицы с рациональными составами рудного и шлакового концентратов, полученных химическим и фазовым анализами, табл. 1.7.
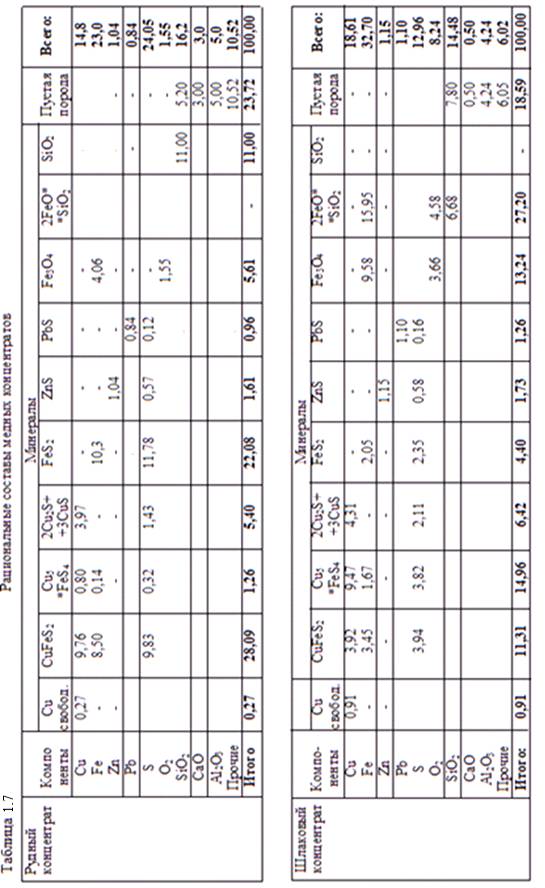
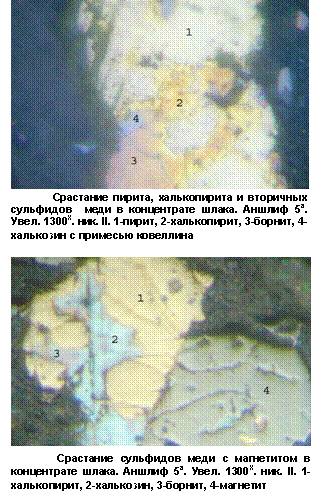
Рис. 1.34 Аншлифы шлакового концентрата , [ 7 ]
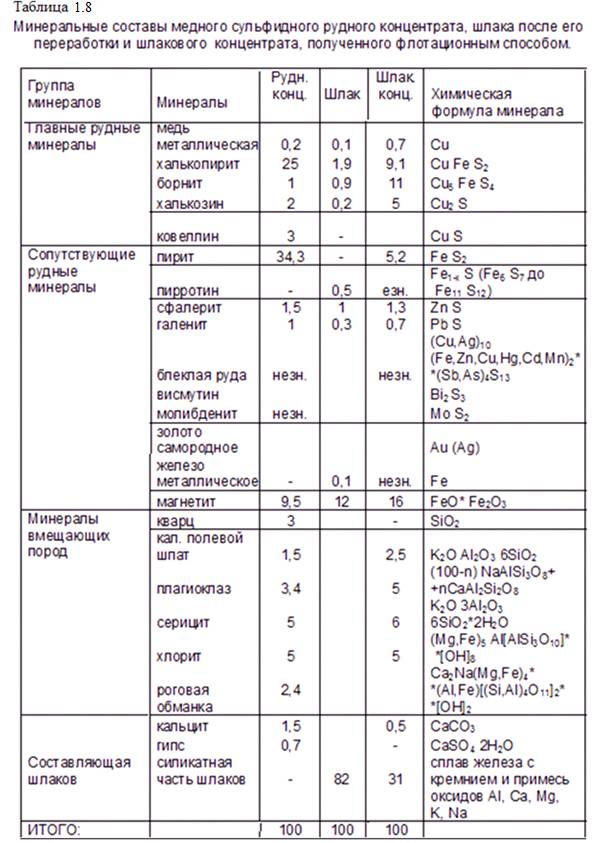
Таким образом, возможен механизм образования борнита в шлаках металлургической плавки рудного концентрата, содержащего преимущественно высшие сульфиды меди, по реакции ( 1 ). Хотя, могут протекать и реакции:
CuS + FeS + 2Cu2S = Cu5FeS4, ( 5 )
0,5 S2 + 2FeS + 5Cu2S = 2Cu5FeS4, ( 6 )
CuS + 2FeS + 5Cu2S = 2Cu5FeS4 + Cu. ( 7 )
Наибольшую вероятность прохождения одной из вышеприведенных реакций могут определить термодинамические расчёты. Результаты, приведенные в таблице 1.9 показывают, что в интервале 673 – 1073 К наиболее вероятно протекание реакции ( 6 ).
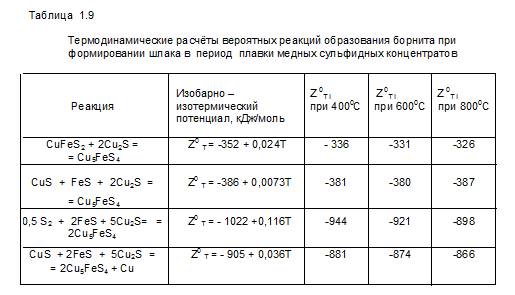
Однако, интерполяция Z0T в сторону роста температур приводит к тому, что при 1473 К (1200 0С) и выше наиболее вероятным становится протекание реакции (7), где из сульфидов меди и железа образуется, кроме борнита, металлическая медь, смотрите рисунок 1.35.
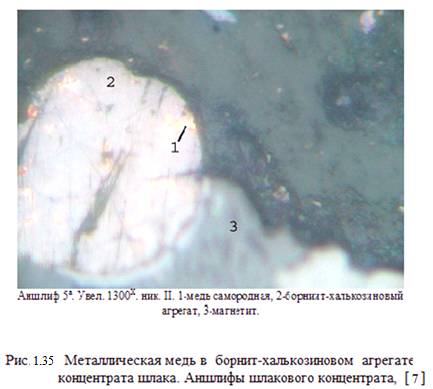
1.6.4. Результаты совместных плавок рудного и шлакового концентратов
Прямая переработка рудного концентрата в смеси со шлаковым приводит к росту потерь меди с «вторичными шлаками». Это хорошо видно по результатам плавок, приведенных на рисунке 1.36.
С увеличением массовой доли шлакового концентрата в общей с рудным концентратом шихте увеличивается в ней и массовая доля высшего сульфида – борнита, протекает его сульфатизация, затем разложение сульфата меди с образованием вторичного оксида меди и, как следствие, растут потери со шлаком плавки меди и драгметаллов.
1.6.5. Окисление и сульфатизация низших сульфидов меди и железа
Низшие сульфиды меди и железа, это: халькозин Cu2S, пирротин FeS и штейн Cu4FeS3 = 2Cu2S + FeS, как сумма двух низших сульфидов разных металлов. Термодинамические расчёты реакций окисления и сульфатизации низших сульфидов приведены ниже, таблицы 1.10 и 1.11.
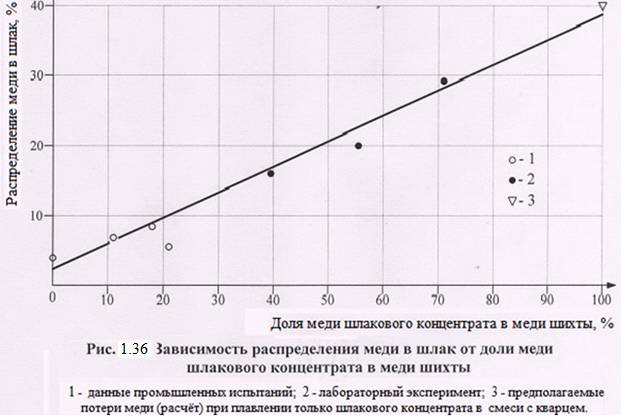
Из таблицы 1.10 видно, что (кроме реакции окисления S8 ) изобарно-изотермические потенциалы реакций окисления серы и низших сульфидов
меди и железа примерно равны:
Z 0T окисления = – 600 + 0,1 Т, кДж/(моль исх.)
Сравнивая соответствующие данные таблиц 1.10 и 1.9, получим, что для
низших сульфидов:
для халькозина ∆ Z= Z 0T сульфатизации – Z 0T окисления = – 725 + 0,67Т, < 0 до 810 0С.
а для пирротина ∆ Z= Z 0T сульфатизации – Z 0T окисления = – 227 + 0,26Т, < 0 до 600 0С.
Как следует из полученных данных, примерно до 700 0С для низших сульфидов более вероятно протекание реакций сульфатизации.
Для полной сульфатизации низших сульфидов, что видно из уравнения первой реакции, приведенной в таблице 1.11, к сульфиду иногда необходимо добавление сернистого газа.
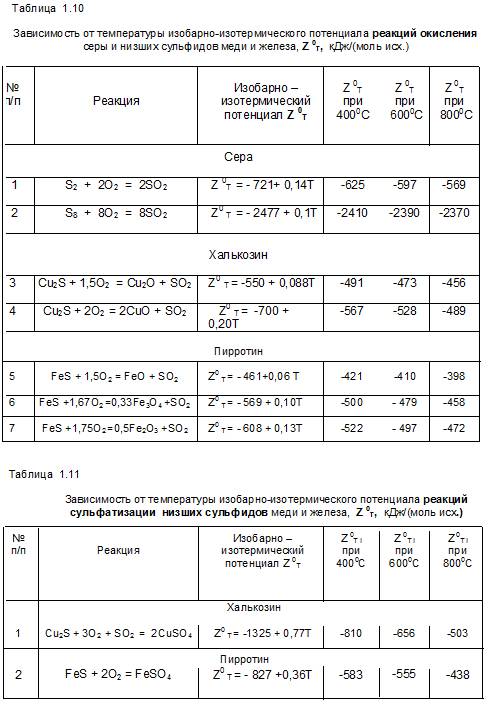
1.6.6. Окисление и сульфатизация высших сульфидов меди и железа
Высшие сульфиды меди и железа: ковеллин CuS, пирит FeS2 , халько-пирит CuFeS2 , кубанит CuFe2S3, твёрдый раствор Cu3Fe4S6, борнит Cu5FeS4 и идаит Cu5FeS6.
Эти сульфиды плавятся в инертной среде при температурах более
900 0 С. При подъёме температуры выше 400 0 С возможна также их диссо-циация с последующим окислением низших сульфидов:
4CuFe2S3 = 2Cu2S + 8FeS + S2 ,
4Cu3Fe4S6 = 6Cu2S + 16FeS + S2,
4Cu5FeS6 = 10Cu2S + 4FeS + 4S2, а также:
2CuS = Cu2S + 0,5S2, при температуре выше 450 0 С,
FeS2 = FeS + 0,5S2 при температура выше 650 0 С,
4CuFeS2 = 2Cu2S + 4FeS + S2 при температуре выше 400 0 С
4Cu5FeS4 = 10Cu2S + 4FeS + S2 при температуре выше 400 0 С.
В общем виде:
4Cuх Feу Sz = 2хCu2S + 4уFeS + (2z – х – 2у)S2 или
Cuх Feу Sz = 0,5хCu2S + уFeS + 0,5 (z – 0,5х – у)S2.
Далее, построим схемы реакций окисления и сульфатизации высших сульфидов меди:
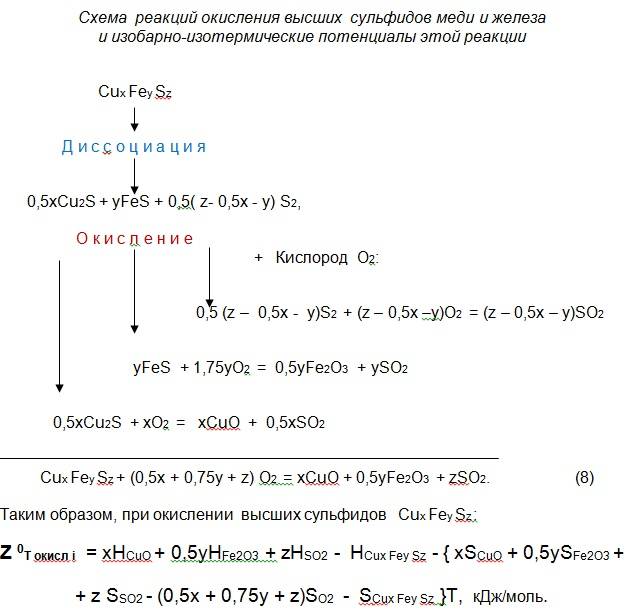
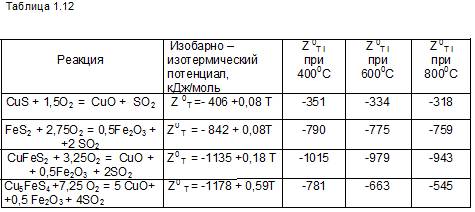
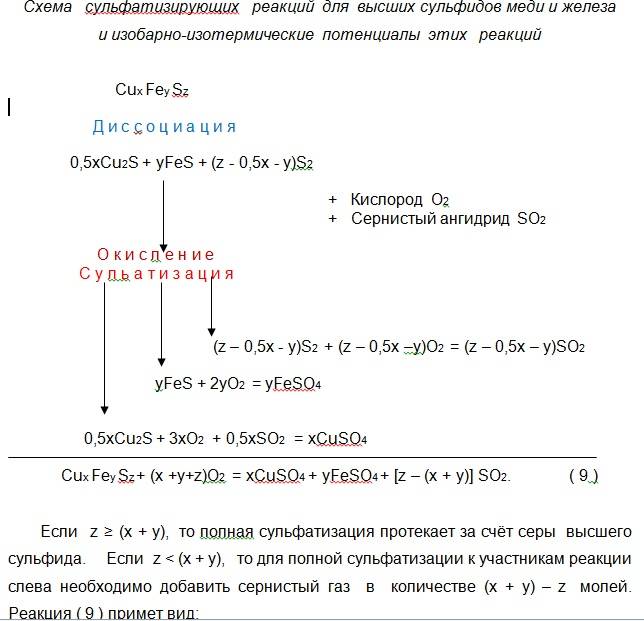

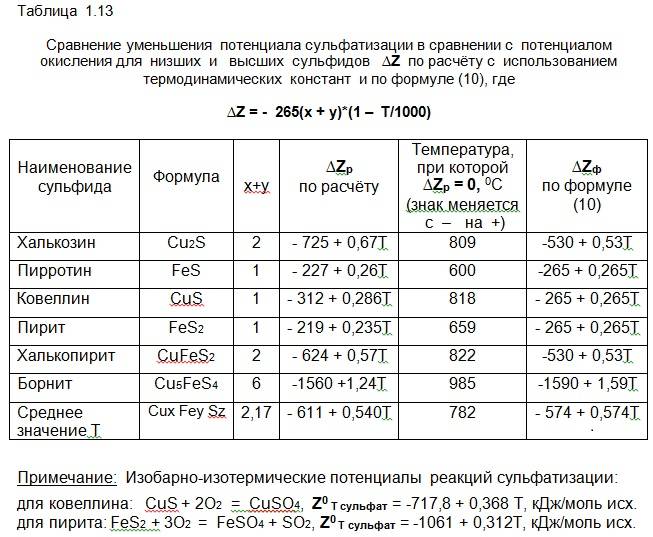
По данным таблицы 1.13 и низшие и высшие сульфиды меди примерно до температуры 782 0С или 1055 К в среде с избытком кислорода вначале сульфатизируются, затем, с ростом температуры, происходит термическое разложение сульфатов (здесь эта часть процесса подробно не рассматривается. а принимается упрощённая схема МеSO4 –> МеO + SO3).
Выполненные расчёты позволяют предположить следующую технологическую схему окисления сульфидов меди и железа в медеплавильном производстве при избытке кислорода, рисунок 1.37.
1.6.7 Выводы
1. Изобарно-изотермические потенциалы реакций взаимодействия сульфидов меди и железа с кислородом (сульфатизирующий обжиг и окисление) имеют отрицательные значения в интересующих нас интервалах изменения
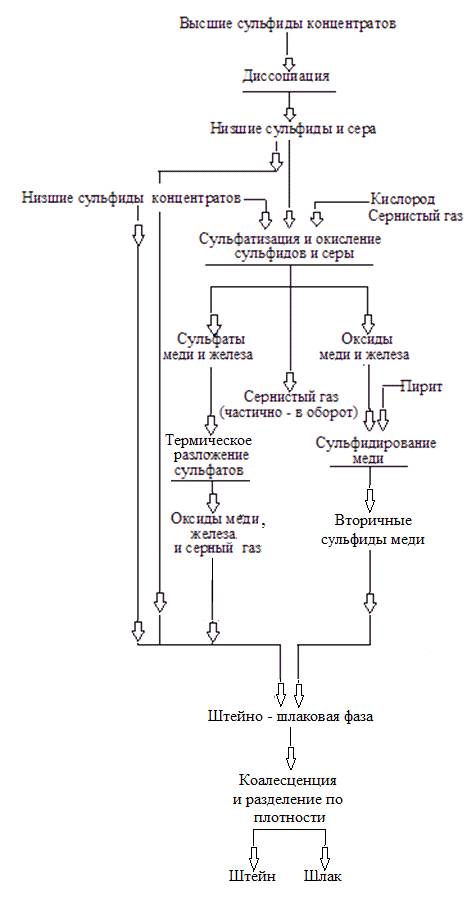

температур – (673 – 1073) К, причём абсолютные значения Z0 соотносятся следующим образом:
Z0 Т сульф. i > Z0 Т окисл.
2. Разница этих потенциалов зависит от числа атомов меди х и железа у в молекуле высшего сульфида, подвергаемого окислению, и от температуры:
∆Z = Z 0T сульф. i – Z 0T окисл i = – 265(x + y)(1 – Т/1000). (В.1)
Отсюда следует, что плавка и обжиг сульфидных медных концентратов, в том числе, например, шлакового, богатого высшим сульфидом – борнитом, в газовой среде с избытком кислорода, будет сопровождаться сульфатизацией, в первую очередь, борнита, а затем других высших сульфидов.
Кроме этого, приведенное уравнение (В.1) показывает, что наименьшая вероятность сульфатизации (в сравнении с окислением) – у ковеллина, пирита и пирротина, затем она повышается для халькозина и халькопирита и становится наибольшей для сложных высших сульфидов – борнита, идаита и других, а также низшего сульфида – штейна.
3. Сульфатизация сульфида меди и (или) железа в сравнении с его окислением требует увеличения расхода кислорода на величину
∆nо2 = 0,25 (2х + у), молей/моль исх.
4. Для оценки превышения величины термодинамической вероятности протекания реакции сульфатизации «нового» высшего сульфида с известным молекулярным составом в сравнении вероятностью протекания реакции его окисления (в металлургическом процессе) нет необходимости знать H°298,15 и S°298,15 высшего сульфида. Оценку можно провести по уравнению (В.1).
5. Если количество атомов серы в молекуле сульфида z равно или больше сумме атомов меди и железа (х + у), то полная сульфатизация протекает за счёт серы высшего сульфида. Если z < (х + у), то для полной сульфатизации к исходным участникам реакции необходимо добавить сернистый газ в количестве [(х + у) – z] молей/моль исх.
6.Таким образом, с ростом массовой доли в металлургической сульфидной
системе высших сульфидов, с увеличением в молекулах этих сульфидов атомов
меди и (или) железа и при избытке кислорода в системе, – при плавке возрастает вероятность протекания реакций сульфатизации и затем (при термическом разложении сульфата меди) образования вторичного оксида меди, что в итоге приводит к увеличению потерь меди со шлаками. Последнее подтверждено практикой.
7. Хотя на вывод 6 может наложить поправки кинетика процессов сульфатизации и окисления сульфидов меди и железа, необходимо уже сегодня, по нашему мнению, ввести понятие сортности высших сульфидных медных концентратов и декларировать её снижение с ростом в них массовой доли меди и железа и увеличением содержания в шихте для плавки таких высших сульфидов.
Снижение сорта медного сульфидного концентрата указывает на повышение вероятности потерь меди со шлаками основного металлургического производства (при прямой переработке таких концентратов).
Список источников, использованных в п. 1.6
1. Мечев В.В., Быстров В.П. и др. Автогенные процессы в цветной металлургии / Металлургия, М.: 1991.– 413 с.
2. Патент РФ № 2255126. Термогидрометаллургический способ комплексной переработки медного концентрата колчеданных руд с извлечением цветных и благородных металлов. Опубл. 27.06.2005.
3. Упрощённый метод расчёта материального баланса плавки сульфидного сырья / Е.И. Калнин, Г.Г. Макарова, В.С. Чахотин // Цветные металлы. 1993. № 6. С. 45 – 47.
4. Технология переработки шлаков отражательной плавки на обогатительной фабрике АО СУМЗ / М. А. Шабалина, В.А. Кравцов и др.// Цветные металлы. 1997. № 2. С.14-15.
5.Санакулов К.С., Хасанов А.С. Шлаки медной промышленности. Ташкент. «ФАН». 2005.
6.Технология переработки шлаков отражательной плавки на обогатительной фабрике АО «СУМЗ» / Шабалина М.А., Кравцов В.А. и др. // Цветные металлы. 1997. №2.С.14-15.
7.Минералого-геохимические особенности распределения меди и железа в концентратах и шлаках МПЗ АГМК / Королёва И.В., Цой В.Д., Мулява Г.С. // Горный журнал Узбекистана. 2009. № 3, стр. – 8.
1.7 Окислительный обжиг молибденитового концентрата
1.7.1 Составление матрицы и обжиг в лабораторной установке
Исследование окисления молибденита в концентрате в гранулированном слое (с добавкой каолина) проводили методом математического планирования эксперимента. Выбрали пятифакторный эксперимент на шести уровнях. Уровни изучаемых факторов приведены в таблице 1.14.
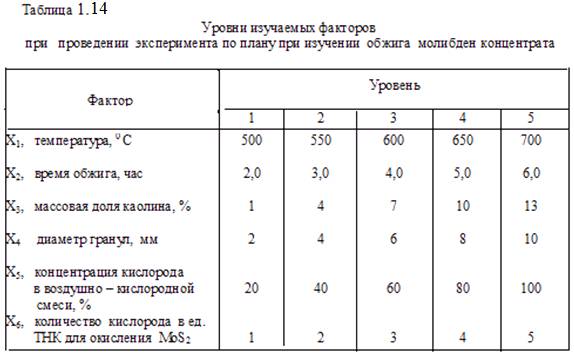
В соответствии с требованиями этого метода составили матрицу, приведенную в таблице 1.15. Для определения расхода кислорода и воздуха на обжиг согласно плану выполнили расчёты, в которых сначала определили необходимые объёмы окислителей (чистого кислорода и, отдельно – кислорода воздуха) затем, исходя из заданного времени окисления, определили объёмные скорости кислорода и воздуха перед смешением для подачи в зону обжига. Результаты расчётов приведены в таблице 1.15.
Исследования проводили в стандартной трубчатой электрической печи с длиной зоны термостатирования 400 мм. Температуру в зоне обжига определяли термопарой ТХА в комплекте с потенциометром КСП – 4 (цена деления шкалы 10 0С). Регулировали температуру в печи (выставляли на заданное постоянное значение), меняя и затем фиксируя электрическое напряжение на входе в печь при помощи трансформатора типа РНО.
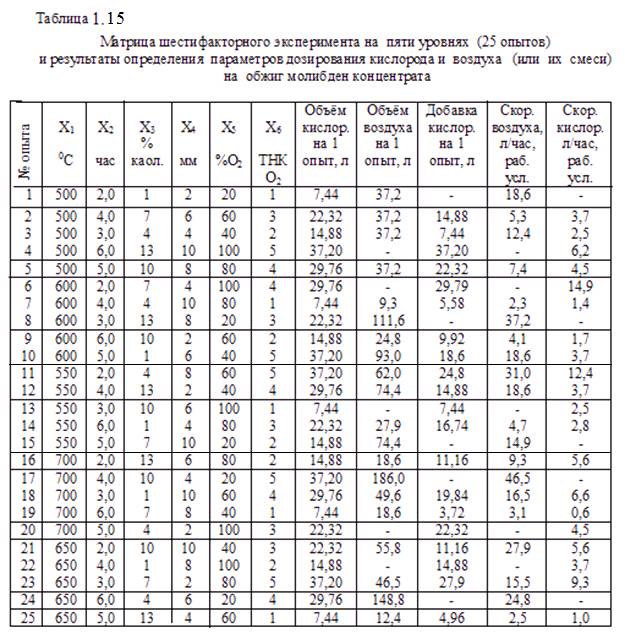
Обжиг проводили в кварцевой реторте, куда помещали в широкой алундовой лодочке гранулированную шихту. Воздушно-кислородную смесь подводили в зону обжига по кварцевой трубке диаметром 6 мм. Продукты реакции отводили по такой же трубке. Их после выхода из реторты охлаждали в воздушном холодильнике и выбрасывали через лабораторную аспирационную систему в атмосферу. Конденсат собирали в приёмник. Воздух и кислород после регуляторов расхода смешивали в колонке с загрузкой обрезками мелких стеклянных трубок (смеситель). Расходы контролировали диафрагмами с тарированными дифференциальными манометрами.
Исследования проводили с молибденовым концентратом, содержащим
молибдена – 40,4 %, серы общей – 33,48 %, рения – 1200 г/т. Для выполнения опытов по плану предварительно взвешивали 25 навесок концентрата массой по 20 г и в них добавляли необходимое количество каолина обогащённого. Смеси увлажняли и вручную формировали гранулы требуемого по плану размера (таблица 1.15). Гранулы сушили на воздухе три дня, отделяли незначительные просыпи и перед загрузкой на обжиг повторно взвешивали.
Лодочку с навеской устанавливали в холодную реторту, закрывали её пробкой с трубками и помещали в разогретую до заданной температуры печь. В момент загрузки температура снижалась, но регулированием напряжения при помощи РНО (вручную) в течение 10 – 20 мин устанавливали заданную и затем подавали на обжиг воздушно – кислородную смесь. С этого момента вели отсчёт требуемого времени обжига.
По окончании обжига прекращали подачу смеси (или чистого воздуха, или – чистого кислорода) и вынимали реторту из печи. После охлаждения на воздухе из реторты выгружали лодочку с огарком, который затем взвешивали. По разнице масс до и после обжига определяли абсолютную потерю массы навески при обжиге. Относили её к начальной массе навески и рассчитывали относительную убыль массы.
Огарки анализировали на содержание серы общей, серы сульфатной, молибдена общего, молибдена, растворимого в аммиачном растворе, дисульфида молибдена и рения.
Результаты определений серы, молибдена и рения в огарках приведены в таблице 1.16. Обработка этих данных позволила установить: степень десульфу-ризации шихты, относительные потери молибдена в возгоны (газы и пыль), степень перевода молибдена в окисленные формы, растворимые в аммиаке, и степень перехода рения в возгоны.
1.7.2 Степень десульфуризации шихты из концентрата и каолина
Степень десульфуризации шихты рассчитывали по формуле:
ŋэ десульф. шихты = 1 – (1 – ΔМ/ М0) * (Sобщ к / Sобщ н), дол. един.,
где: ΔМ/ М0 – убыль массы навески гранул шихты при обжиге, дол. един.,
Sобщ н – начальное содержание серы в шихте (до обжига), определяется
с учётом степени «разубоживания» концентрата каолином, %,
Sобщ к – конечное содержание серы в огарке, %.
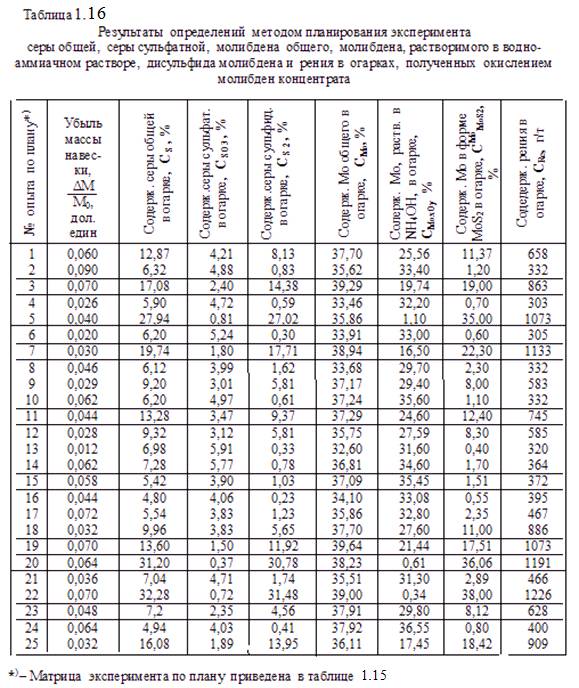
Результаты расчётов экспериментальной степени десульфуризации шихты ŋэ при обжиге по плану приведены в таблице 1.17.
По данным ŋэ составлена таблица 1.18, где приведены экспериментальные значения частных функций Y1,…Y6 от, соответственно, факторов Х1, … Х6 .
Результаты таблицы обработаны методом наименьших квадратов, определены частные функциональные зависимости и установлены их значимости вычислением коэффициентов корреляций. Получено, что для Y1, Y2, Y3 и Y4 коэффициенты корреляции < 0,3, что говорит о незначимости этих функций.
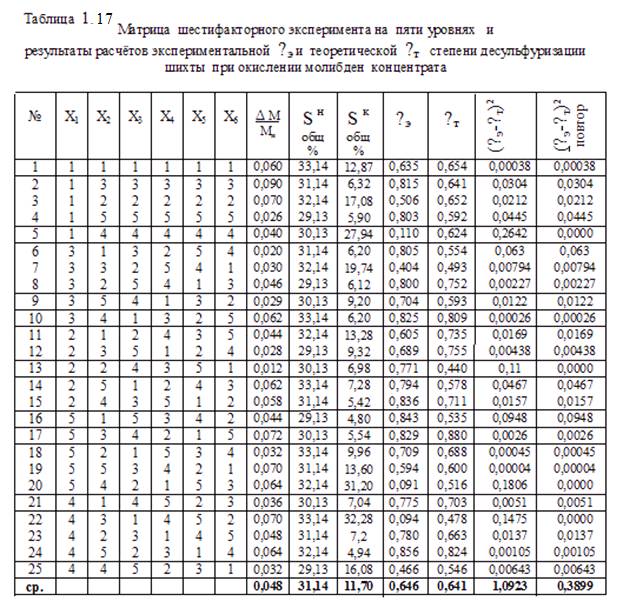
Для Y5 и Y6 коэффициенты корреляции равны, соответственно, 0,974 и 0,850. Частные уравнения:
Y5 = 0,83 – 0,0013 Х5,
Y6 = 0,5025 + 0,0475 Х6.
Обобщённое уравнение:
У = (Ycр * Ycр * Ycр * Ycр * Y5* Y6 )/ (Ycр )5 = (Y5* Y6)/ Ycр =
= (0,83 – 0,0013 Х5)*( 0,5025 + 0,0475 Х6)/0,646, или
У = 0,6457 – 0,00244 * Х5 + 0,061 * Х6 – 0,00023 * Х5 * Х6. ( 10 )
или ŋэ десульф. шихты = 0,6457 – 0,00244*СО2 + 0,061*ТНКО2 – 0,00023*СО2* ТНКО2.
.
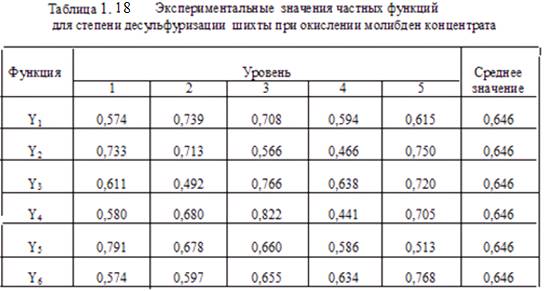
Ошибка уравнения (10), согласно расчётам в таблице 1.17 и по формулам в [1], – 23,98 %. Если применить правило Кайзера, [1] , отбросить четыре значения ŋэ в опытах 5, 13, 20 и 22, как грубые, и принять их равными теоретическим значениям ŋт, то ошибка уравнения ( 10 ) составит 14,33 %.
Таким образом, нами получены экспериментальные данные и уравнение, из которых следует, что основными факторами, влияющими на степень десульфуризации шихты из молибденового концентрата и каолина, являются концентрация кислорода в воздушно – кислородной смеси СО2 и количество кислорода в единицах ТНК для окисления MoS2 в концентрате – ТНКО2 по уравнению