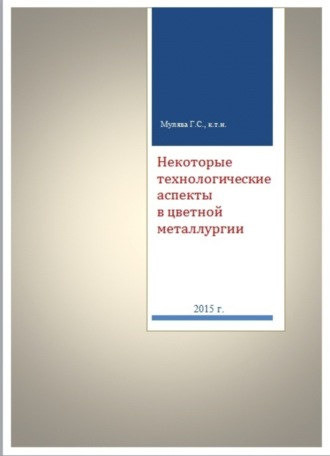
Некоторые технологические аспекты в цветной металлургии
Установлено (рис. 1.22), что коэффициент теплообмена в вибрируемом слое флотационного концентрата (состав – в таблице 1.1) в низком вакууме линейно зависит от отношения частоты вибрации f к частоте собственных колебаний слоя fс , когда его порозность ε равна 0,7:
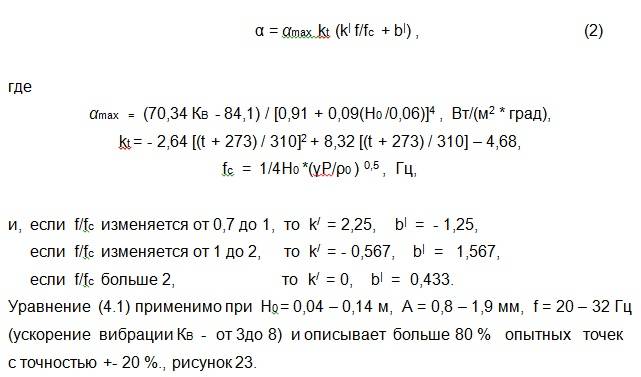
Сопоставлением результатов исследований теплообмена и гидродинамики вибрируемого слоя концентрата в вакууме установлены четыре области теплового и гидродинамического соответствия и получены уравнения для определения давлений газа, разграничивающих эти области.
Нагрев концентрата в вибрируемом слое рекомендуется проводить при положительном статическом перепаде давления газа при
Р = 7,7Н0 2 ρ0 f2 , Па,
когда частота вибрации f примерно на 20% превышает частоту собственных: колебаний слоя. Коэффициент теплообмена при этом будет на 12,5% меньше αmах в этих условиях.
В результате исследований по теплообмену концентрата и с привлечением литературных данных для других материалов получено обобщенное уравнение


для определения частоты вибрации, обеспечивающей максимальные коэффициенты тепло – и массообмена в слое:
____________
fопт = (n/4H0) [(1 – ωε0) / (1 – ε0)] (γP/ρт)/(1 – ε/), Гц, n = 1, 2, 3 …
где ω – степень расширения слоя при α = αmах и ε/ – порозность слоя с модулем упругости, равным модулю упругости газовой среды (ε/ > 0,8).
1.1.5 Виброкипящий слой. Обсуждение результатов.
Сопоставим на одном рисунке (рис. 1.24) зависимости от давления Р коэффициента теплообмена α и статического перепада давления газа (воздуха)
∆Рст. Эти кривые – типичные и при их анализе можно различить четыре области характерного соответствия между гидродинамикой слоя и теплообменными процессами в нём (сравните, например, рис. 1.6 и рис. 1.22):
В области I ∆Рст ≈ 0, давление газа меньше Р0 ≈ (0,7 – 1,4) кПа и, так как при этом расчётное значение fс << f, которая обычно превышает 15 – 18 Гц, то, согласно (2), α = 0,433 αmax.
В области II статический перепад отрицательный, ∆Рст < 0, α < 0,433 αmax, а границы области – от Р0 до Р*1 , причём последнее определяется по формуле:
Р*1 = (16Н0 2 ρ0 f2 / γ)[(1 – ε0)/(1 – εв1)] 2,
когда Н0, ρ0 и ε0 – параметры свободно насыпанного слоя, а εв1 = 0,488.
В области III статический перепад положительный, ∆Рст > 0, коэффициент теплообмена увеличивается от 0,433 αmax до αmax, а интервал давлений составляет от Р*1 до Р α max , которое примерно равно Р*2 :
Р*2 = (16Н0 2 ρ0 f2 / γ)[(1 – ε0)/(1 – εв2)] 2,
причём εв2 = 0,724; кроме этого:
Р α max ≈ 0,8 Р*2.
В большей части области III
∆Рст+ = ∆Рст max + .
Наконец, в области IV ∆Рст+, быстро уменьшаясь, достигает отрицательных значений, что, как и в области II, сопровождается снижением интенсивности теплообмена.
Хотя резонансные явления возникают в широком диапазоне давлений газа,
(∆Рст+ зафиксирован от Р*1 до Р*2 ), отмечен для давления воздуха до атмосферного Р ≈ 95 кПа лишь один максимум на кривой α (Р), чему соответствует порозность слоя ε ≈ 0,7. По – видимому, при Р < Р α max , когда
εв < 0,7, степень расширения слоя и интенсивность его перемешивания недостаточны для достижения αmax. Наоборот, при Р > Р α max, (0,7 < εв < 0,724),
происходит значительное расширение слоя, он насыщается газом и возрастает термическое сопротивление между частицами. Коэффициент теплообмена α вновь уменьшается.
Аналогичное прохождение кривой коэффициента теплообмена через максимум известно в исследованиях по кипящему слою, [ 9 ].
Список источников, использованных в п. 1.1
1. Членов В.А., Михайлов Н.В. Явление возникновения статического перепада давления газа в виброкипящем слое. Открытие / Приоритет от 04 июля 1963 г. Диплом №138.
Также: Явление возникновения статического перепада давления газа в виброкипящем слое. [Административный ресурс] http://nplit.ru/books .
Также: Выдержка из книги «Конюшая, «Открытия советских учёных» [Административный ресурс] http://www.ngpedia.ru/cgi-bin/ .
2. Виброкипящий слой / В.А. Членов и Н.В. Михайлов – М.: Наука, 1972.
3. Контроль пылеулавливающих установок / Г.М. Гордон и И.П. Пейсахов – М.: Металлургия, 1978.
4. Краткий справочник химика. – М.: Химия, 1979.
5. Коузов П.А. Основы анализа дисперсного состава промышленных пылей и измельчённых материалов – Л.: Химия, 1974.
6. Измерения в дисперсных системах /Б.И. Леончик и В.П. Маякин – М.:Энергия, 1971.
7. Промышленное псевдо ожижение / Д. Кунии и О. Левеншпиль – М.: Химия, 1978.
8. Аппараты со стационарным зернистым слоем. Гидравлические и тепловые основы работы / М.Э. Аэров, О.М. Тодес и Д.А. Наринский – Л.: Химия, 1979.176 с.
9. Стрелков. С.Г. Введение в теорию колебаний. – М.: 1964.
10. А. с. 1497459, СССР, МКИ'^ G01 Н13/00. Способ определения частоты собственных колебаний материала / А.Ф. Рыжков, М.Г. Зайцев, Г.С. Мулява,
В.А. Микула, А.С. Колпаков и др. (СССР). – № 4351758/ 25-28; заявл. 29.12.87; опубл. 30.07.89, Бюл. № 28. – 3 с: ил.
11. Мулява Г.С. Вакуум-термическая переработка ртутно-сурьмяных концентратов в виброкипящем слое / Автореф. канд. дисс. – Орджоникидзе, – СКГМИ, – 1985.
12. Кальтман И.И., Тамарин А.И. Исследование теплопереноса между вибропсевдоожиженным слоем дисперсного материала и охлаждаемым в нём телом / ИФЖ, – 1969, – т.15, №4.
13. Мулява Г.С. Определение критерия Кнудсена в меж зерновом пространстве вибрируемого слоя дисперсного материала в вакууме / В сб. «Процессы цветной металлургии при низких давлениях». – М.: «Наука», – 1982, стр. 20 – 24.
1.2 Сушка ртутно – сурьмяного флотоконцентрата в виброслое
Известно, что при суше мелкодисперсных материалов в виброкипящем слое при кондуктивном тепло подводе температурный градиент по высоте слоя практически отсутствует, температура материала в период постоянной скорости сушки близка температуре мокрого термометра, а переход к периоду падающей скорости наступает при влагосодержании, меньшем равновесного. Для слоя концентрата ниже показано, что сушка материала в виброкипящем слое практически завершается по истечении периода постоянной скорости процесса.
Принята следующая методика определения времени сушки концентрата в низком вакууме: продолжительность постоянного значения температуры слоя считали равной периоду сушки с постоянной скоростью и временем выхода всей влаги из слоя. Кроме того, улавливали и измеряли массу сухой пыли, определяя пыле вынос при интенсивном парообразовании.
Эксперименты проводили на установке, содержащей герметичную цилиндрическую камеру, окруженную зашитым в свинцовый блок змеевиком, по которому прокачивалась вода заданной температуры из термостата, рисунок 1.25.
Блок с камерой закреплен на столе вибростенда с регулируемыми частотой и амплитудой вибрации. Вакуумный насос с краном – натекателем на всасывающем патрубке и воздушный холодильник обеспечивали требуемое давление пара в камере. Разность температур материала и стенки камеры фиксировали, получая дифференциально-термическую кривую процесса сушки, на которой период достоянной скорости изображался в виде горизонтального участка.
Типичная диаграмма записи температуры стенки камеры tст в процессе сушки и разности температур стенки камеры и материала tст – tм = ϑ приведена на рисунке 1.26.
Результаты экспериментов и вычисленное по ним первое критическое влагосодержание Uкр , выход влаги в период постоянной скорости сушки и численное значение последней, Nc , приведены в таблице 1.2. Полученные данные – сравнительно низкое значение первого критического влагосодержания ( ≈ 0,33%) и, соответственно, высокий выход влаги из слоя в период постоянной скорости сушки ( ≈ 94 %) позволили составить методики расчётов интенсивности испарения влаги, интенсивности пылевыделения и коэффициента теплообмена.





Исследования проводили по плану, выбрав изменение шести факторов на двух уровнях. Характеристика плана экспериментов по исследованию процесса сушки концентрата приведена в таблице 1.3.
Согласно принятым значениям Кв и Р, частота вибрации и температура стенки камеры на верхнем и нижнем уровнях составляли: f = 30,8 и 25,5 Гц для
А = 0,84 мм и f = 24,5 и 20,5Г ц для А = 1,32 мм; tст = 61,6 и 44,5 °С для
∆t = 10 °С и tст = 71,6 и 54,5°С для ∆t = 20°С.
По опытным значениям времени в период постоянной скорости сушки, массе сухого материала в камере и пыли после сушки и действительному температурному перепаду между слоем и стенкой определяли интенсивность
испарения влаги jB, интенсивность пыле выноса jП и коэффициент теплообмена при сушке α суш.
Обработка результатов на ЭВМ показала, что с коэффициентами корреляции, не меньшими 0,7,они описываются степенными функциями:

1) – Разность температур стенки камеры и мокрого термометра.
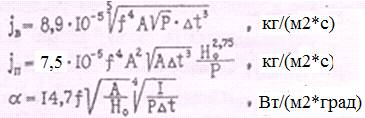
Приведенные зависимости использованы при решении дифференциальных уравнений процесса сушки, что позволило получить уравнение для определения времени сушки концентрата в вибровакуумной установке с учетом уноса части материала в виде пыли:

где ρ0 – насыпная плотность слоя, индекс о – начальное состояние.
1.3 Оптимальные условия возгонки сульфида ртути из ртутно – сурьмяного
флотоконцентрата в виброслое
При обосновании параметров вакуум-термической технологии с целью проведения процесса в оптимальных условиях выбрана модель реактора, в которой сушка, нагрев материала и его выдержка для полного удаления летучих (сульфида ртути или киновари) проводятся на внутреннем виброконвейере при одинаковых манометрическом и вибрационных параметрах.
Греющие стенки термостатированы и по температурному режиму разделены на две зоны – в первой зоне (сушка) температура стенок на ∆t 0C превышает температуру материала, почти равную «точке кипения» воды; во второй зоне (нагрев слоя до «точки кипения» киновари и выдержка до полного удаления HgS) температура стенок превышает «точку кипения» киновари, принимаемую за температуру огарка, на 2 – 5 %.
Кроме того, на параметры вибрации наложены ограничения, обеспечивающие заданный пыле вынос в процессе сушки концентрата и положительный статический перепад давления газа в сухом виброслое с целью создания минимального диффузионного сопротивления. Исследование влияния гидродинамики на массообменные процессы в слое концентрата проведено методом ДТА (применявшимся для изучения процесса сушки) путем добавки в слой сухого материала мелких кристаллов СuSO4*5Н2O и регистрации скорости удаления влаги при разложений кристаллов.
Установлено, что при положительном статическом перепаде давления газа в слое время на удаление влаги при разложении кристаллогидрата сульфата
меди значительно ( в 3 и более раз) меньше, чем при отрицательном.
Показано, что если температуру слоя флотоконцентрата в процессе обжига поддерживать равной «точке кипения» киновари, то вакуумирование приводит к незначительным потерям сурьмы (1 г/кг ртути), что позволяет не учитывать их при оптимизации процесса.
В качестве критерия оптимизации выбрана сумма удельных энергозатрат на переработку концентрата ∑qi , которая включает затраты на создание вакуума, нагрев материала, тепловые потери и т.д. За аргумент оптимизации приняли давление в реакторе Р, как одну из наиболее легко регулируемых величин. Для дополнительных условий: ширина полки виброжёлоба равна
начальной высоте слоя, скорость движения материала и относительное
ускорение вибрации постоянны, получены графические решения уравнения
d ∑qi / dP = 0,
(здесь d – знак дифференциала).
Из решения следует, что для проведения процесса вакуум-термической переработки ртутно-сурьмяного концентрата с минимальными энергозатратами. (200 кВт*час/т) давление в реакторе необходимо поддерживать в два раза больше суммы давления насыщенных паров воды в холодной части конденсатора и гидравлического сопротивления линии откачки. куда входят, кроме вакуумных трубопроводов – обогреваемые пылевая камера и циклон:
РОПТ = 2(РН + ∆PГ).
Оптимальная частота вибрирования слоя равна:
fопт = [(Pопт / 6224)0,5] / [Н0 (1 – x)] , Гц,
и оптимальная амплитуда вибрации:
Аопт = 1,56*106 [КВ Н02 (1 – х)2] / Ропт, мм,
причем допустимое влагосодержание концентрата определяется из соотношения:
U0 доп = 11,36 [1 – (1 – x)2,75] / (Aопт2 ∆t), кг/кг,
где х – заданный пыле вынос из слоя при сушке, дол. ед.
На основании проведенных исследований и с распространением данных по интенсивности испарения киновари из слоя с малым диффузионным сопротивлением,1), на виброкипящий слой при ∆Рст > 0 получены уравнения для расчета времени пребывания концентрата в реакторе при оптимальных условиях переработки.
Построены номограммы для определения временя переработки и величины пыле выноса из слоя в зависимости от исходного влагосодержания концентрата, содержания в нем киновари и относительного ускорения вибрации, если Ропт = 5300 Па (40 мм рт. ст.), f = 24 Гц, Н0 = 0,04 м и ∆t = 20°С. Номограммы приведены на рисунках 1.27 и 1.28.
_________________________
1) – Зайцев М.Г. Вакуум-термический способ переработки ртутно-сурьмяных концентратов/ Автореф. канд. дисс. – Орджоникидзе, – СКГМИ, – 1979.
1.4 ДТА пироантимоната ртути Hg2Sb2O7

Рис. 1.29 Здесь исследуют свойства солей ртути
Нами в 2010 году был по новой технологии получен пироантимонат ртути, который исследовали – нагрели со снятием Т и ДТ – кривых при медленном линейном подъёме температуры в печи.
Схема установки и схема измерений температур во времени приведены, соответственно, в частях а) и б) рисунка 1.30. Установка была изготовлена герметичной и таким образом, чтобы иметь возможность проводить нагрев образца и эталона в заданной газовой среде и конденсировать и улавливать пары ртути. На рис. а) показано, что железный блок 3 с ампулами для эталона (прокалённый кварцевый песок) и образца (пироантимонат) помещён в кварцевую пробирку 10, герметично соединённую с металлическим корпусом 9, который сбоку снабжён отсасывающим патрубком 8. На рисунке размеры корпуса 9 и его деталей непропорционально увеличены относительно размеров печи 1.
Подъём температуры в печи осуществляли плавным увеличением напряжения от трансформатора, ползунок которого перемещался вращением оси редуктора с задаваемым и ступенчато регулируемым числом оборотов. Скорость
нагрева печи поддерживали, как правило, равной 1,5 град./мин. Система
улавливания и очистки газов от ртути, как и трансформатор, на рис. а) не
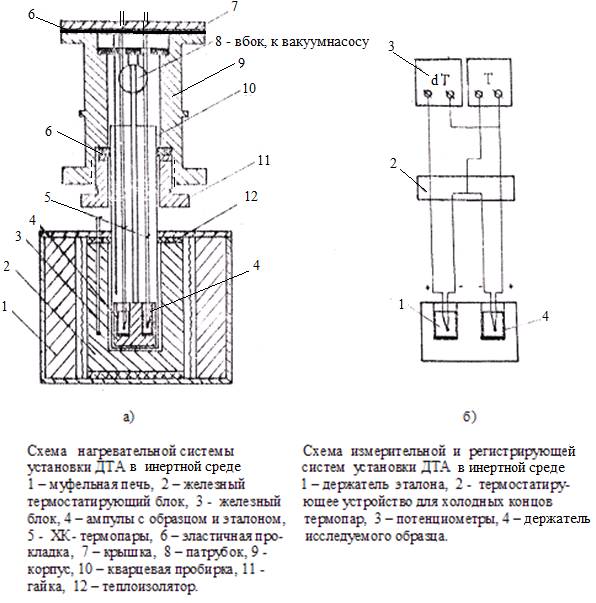
Рис. 1.30 Установка для проведения ДТА
показаны. Температуру в образце и эталоне измеряли термопарами ХК (диаметры проволок по 0,3 мм). В термостатирующем блоке 2 контроль
температуры осуществляли термопарой ХА, имеющей диаметр проволок по 0,6 мм. Холодные концы термопар (см. схему б) термостатировали.
Температуру холодных концов измеряли ртутным термометром с точностью +– 0,1 0С. Термопары включали по схеме, приведенной на рис 30.б). Разность температур в образце и эталоне после преобразования её в ЭДС измеряли микровольт метром (тип – КСП– 4М) с ценой деления шкалы 10 мкВ и диапазоном – 100 + 900 мкВ. Температуру в образце после преобразования в ЭДС измеряли потенциометром класса 0,05 с ценой деления шкалы 25 мкВ методом компенсации (на рис. б) не показан). Не скомпенсированную ЭДС измеряли микровольт метром типа КСП-4М. Принятая схема измерения температур обеспечила чувствительность и точность метода, соответственно, не хуже 0,10С и +– 0,15 0С
Установку ДТА проверили по известной методике (измерили температуры кипения воды и ртути). Получили удовлетворительное схождение с табличными данными, 0С: для воды, соответственно 98,4 и 98,3 для ртути – 353,5 и 353,2 (давление инертного газа – аргона в пробирке 10 уравняли с атмосферным – 715 мм рт. ст., которое поддерживали постоянным в течение измерений).
Изменение во времени температуры образца, t, 0С, и разности температур эталон-образец, dt, 0С, при нагреве блока с постоянной скоростью, когда образцом является Hg2Sb2O7, приведено на прилагаемых ниже кривых, рисунок 1.31.
При 573 0С на dt – диаграмме был зафиксирован небольшой положительный тепловой эффект, что соответствует переходу кварца из α – модификации в β – модификацию. Затем, примерно при 705 0С, появляется второй незначительный экзо эффект, который можно связать с перестройкой кристаллической структуры образца. При 726 0С начинает формироваться эндо эффект, что показывает на появление и затем развитие процесса разложения пироантимоната: 2 Hg2Sb2O7 = 4HgП + 2Sb2O4 + 3O2 .
Наибольшую скорость разложения образца зафиксировали при 786 0С.


1.5 Кальцинирующий обжиг известняка в ТВП и шахтной печи. Балансы.
ТВП – трубчатая (или – барабанная) вращающаяся печь.
Обжиг известняка с целью термического разложения большей части карбоната кальция на оксид кальция и углекислый газ в настоящее время при заводах цветной металлургии, нуждающихся в извести, проводят в трубчатых вращающихся печах (ТВП) или шахтных печах (ШП). Основное различие в аппаратурном оформлении является следствием разного вида взаимодействия массы кусков известняка (затем, по мере обжига, извести) с потоком воздуха и технологических газов: в ТВП – в горизонтально пересыпающемся и продуваемом слое, в ШП – в плотном вертикально перемещаемом, также продуваемом слое.
Технологическая схема обжига известняка в шахтной печи (которая, как частный случай, включает в себя и схему обжига в трубчатой вращающейся печи) приведена ниже на рисунке 1.32, где виден порядок основных операций.
С точки зрения экономии энергии это: продувка горячего слоя извести воздухом, направляемым затем в зону горения природного газа и продувка слоя свежих (вначале холодных) порций известняка горячими технологическими газами. Утилизация тепла от обожжённой извести и технологических газов в шахтной печи выгодно отличает её от ТВП, где, хотя и существует схема противоточного движения материала и воздуха (газов), но эффективность тепло – массообменных процессов в пересыпающемся слое значительно ниже, чем в продуваемом плотном слое в ШП.
Для количественного анализа эффективности двух схем обжига известняка провели расчёты обжига известняка при условиях, приведенных ниже в таблице 1.4 сравнительных исходных данных. Исходные данные подобраны практически идентичными, а производительность агрегатов равна 1,9 +– 0,1 кг СаО/с [или – (17+-0,9) т известняка/час или – (432 +– 22) т известняка/сут].
Учтена и специфика процессов. Например, продуваемый слой ШП максимально использован для утилизации тепла от сжигания природного газа.
Результаты расчётов приведены в форме балансов масс и тепла, отнесённых к 1 кг производимого оксида кальция.


Таблица 1.4.Сравнительные исходные данные для обжига известняка в двух типах печей

Как видно из данных в таблицах 1.5 и 1.6, удельный расход природного газа на процесс в шахтной печи почти в два раза меньше, чем в трубчатой печи. Отсюда и соответствующая разница в нагрузках на агрегаты по воздуху.
«Правильное» аппаратурное оформление кальцинации известняка (обжиг в ШП) почти в два раза снижает выброс в атмосферу технологических газов и в два раза уменьшает пыле вынос.
Правда, проведение обжига в ТВП имеет свои преимущества в сравнении с обжигом известняка в ШП: на порядок проще система контроля и автоматизации, значительно больше межремонтный срок эксплуатации ТВП и сопутствующих агрегатов. В трубчатой печи также значительно меньше риск образования настылей.

1.6 Окислительная плавка медного сульфидного концентрата
с добавкой шлакового
В основе известных пирометаллургических процессов получения меди обжигом и плавкой сульфидных медных концентратов лежат реакции окисления в них кислородом высших сульфидов меди и железа (халькопирита, пирита). Это позволяет получить дополнительную теплоту и, подняв температуру шихты, перевести её в жидкое состояние. Последнее даёт возможность сформировать из образующихся низших сульфидов меди и железа штейн, выделив затем его из шлаковой фазы.
Большую роль в этих процессах играет дозирование кислорода, наличие в шихте горючей (элементной) серы от диссоциации высших сульфидов и, затем, после формирования и перехода в жидкое состояние всей технологической массы – её вязкость. Точнее – наличие в системе тугоплавких соединений. С ростом массовой доли в шихте таких соединений (магнетита), а, следовательно, вязкости, ухудшается коалесценция жидких сульфидов и растут потери со шлаком меди и растворённых в её соединениях золота и серебра.
Граничное содержание меди в шлаке, когда он переходит в разряд «отвальный», с течением времени меняется и, очевидно, определяется экономическими показателями в регионе в данный момент времени. Как правило, эта граница постепенно снижается и сегодня шлаки из «старых» отвалов с массовой долей меди (0,8 – 1,0)% вовлекают в переработку.
Известное производство переработкой таких шлаков измельчением, флотацией и затем плавкой получаемого шлакового концентрата в основном металлургическом переделе в смеси с рудным концентратом позволяет говорить о пирометаллургии техногенной сульфидной меди.
Особенности такой пирометаллургии рассмотрены в настоящей части предлагаемой работы.